Reliability modeling is usually more complex for repairable systems. Often, methods like Markov models (chains ) is required to adequately model repairable systems as opposed to simple series block diagram methods for non-repairable systems. In the area of monitoring or analysis, the following table compares methods for both types of systems.
In order to address the reliability characteristics of complex repairable systems, a process is often used instead of a distribution. The most popular process model is the Power Law model. This model is popular for several reasons. One is that it has a very practical foundation in terms of minimal repair.
The Power Law model is often used to analyze the reliability of complex repairable systems in the field. The system of interest may be the total system, such as a helicopter, or it may be subsystems, such as the helicopter transmission or rotator blades. When these systems are new and first put into operation, the start time is 0. Repairable system reliability (and similarly, a safety mishap process) is the result of the interplay of complex factors and conditions. One approach to modeling a complex system is to use a simplified model. Models for the reliability of repairable systems must account for the occurrence of.
Often, these event times or interevent times are not independent and. This is the same as assuming that the system is AS-GOOD-AS-NEW after the repair, which is not true in repairable systems in general. In most cases, the system is AS-BAD-AS-OLD after the repair. This is particularly true for large systems, where replacing a component does not have a great impact on the system reliability.
For repairable systems, maintenance plays a vital role in the life of a system. Generally , maintenance actions can be divided into three types: corrective maintenance , preventive maintenance and inspections. Several researchers have presented a few calculation or estimation techniques to achieve repairable system reliability.
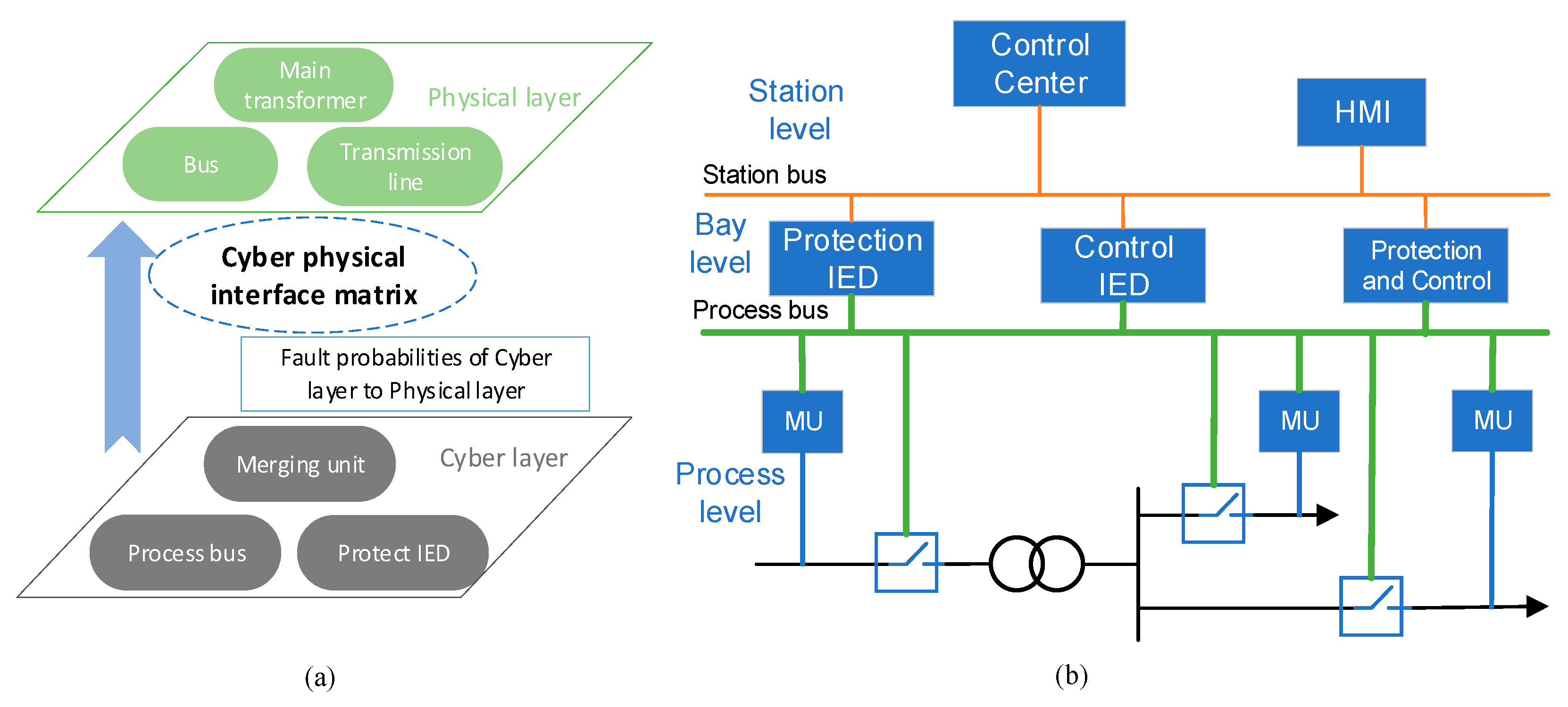
This article explains the mean cumulative function (MCF) as a powerful and easy technique to estimate and monitor repairable system reliability. In reliability engineering calculations, failure rate is considered as forecasted failure intensity given that the component is fully operational in its initial condition. In this appendix, we will present the two methods used in the RGA software to estimate the confidence bounds for Repairable Systems Analysis.
The Fisher Matrix approach is based on the Fisher Information Matrix and is commonly employed in the reliability field. A unique, practical guide for industry professionals who need to improve product quality and reliability in repairable systems. Owing to its vital role in product quality, reliability has been intensely studied in recent decades.
The USAF generally does not know the reliability of its fielded repairable systems. The reported metric, Mean Time Between Failure (MTBF), is too lagging to be actionable in the best case, and is not representative of actual system reliability in the worst case. This means system reliability degraded quickly in that period and needs to be investigated.
After that, system reliability improves in the period from 1days to 2days, which is reflected by a decreasing ROCOF. System reliability degraded again from 2days to 3days and finally improved thereafter. The reliability literature is rich in studies related to repairable systems modelled through renewal processes and most particularly by homogeneous Poisson processes (HPP). Nevertheless, the hypothesis behind a renewal process inherently precludes representation of repairable system ageing. During this correct operation, no repair is required or performe and the system adequately follows the defined performance specifications.

A repairable system is one which can be restored to satisfactory operation by any action, including parts replacements or changes to adjustable settings. When discussing the rate at which failures occur during system operation time (and are then repaired) we will define a Rate of Occurrence of Failure (ROCF) or repair rate. The Pattern of Failures with Time (Non- Repairable Items) There are three basic ways in which the pattern of failures can change with time.
The hazard rate may be decreasing, increasing or constant. Repairable System Apportionment Another reliability allocation metho called Repairable Systems apportionment, is designed for repairable systems. Since this circuit is usually not repairable , we will not apply this method to the example discussed above.

The algorithm is, however, briefly discussed next.
No comments:
Post a Comment
Note: Only a member of this blog may post a comment.